The manufacturing landscape is an ever-evolving space driven by advances in production technology, machine tools, information technology, materials, and products. One of the newest advancements in manufacturing is 3D printing and additive manufacturing. 3D printing is a way of making real, 3D objects from a digital design – by building them layer by layer using materials like plastic, metal, or resin. 3D printing and additive manufacturing refer to the same thing, a process where objects are made layer by layer. It is called additive manufacturing as it involves adding material layer by layer unlike traditional manufacturing (like cutting or drilling), which removes material.
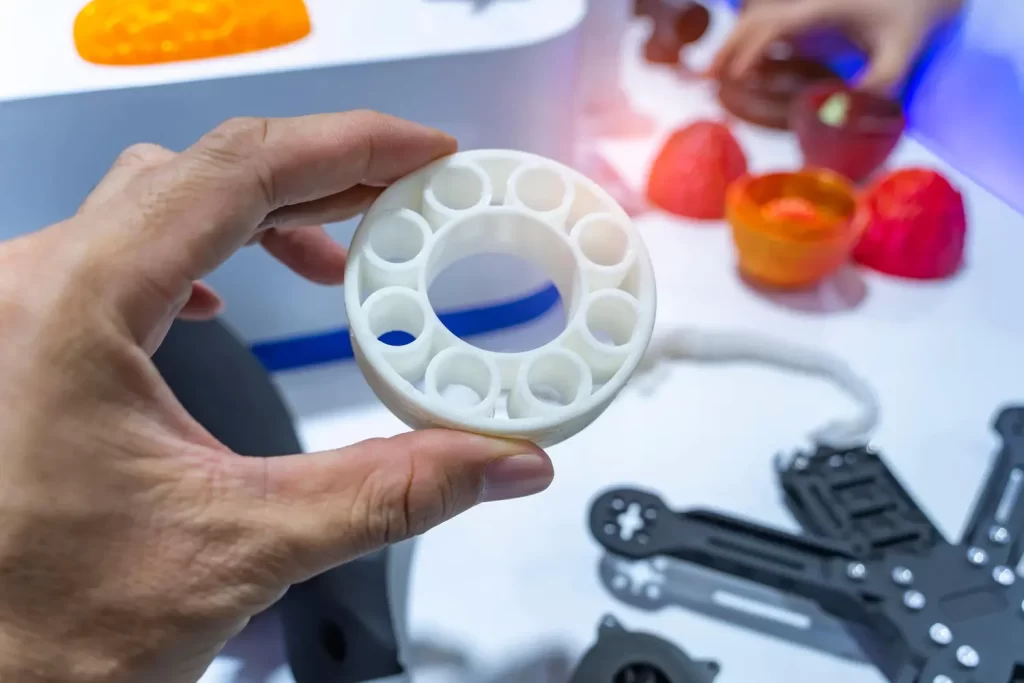
How does it work?
- Design: A 3D model of a bearing is created on a computer.
- Print: The printer builds the bearing layer by layer using various materials.
- Finish: Once printed the bearing may go through polish, heat treatment, etc.
How 3D Printing Is Used in Bearing Production?
3D printing is mainly used to make bearing parts or full bearings for special applications – not for mass production. The 3D models are created using software, further depending upon the bearing’s use material is chosen, post-selection the printer starts building the bearing layer by layer. After printing the bearing may require post-processing involving polishing, heat treatment, assembly, etc. The bearings manufactured are especially useful in research, development, or custom machines. 3D printing is used in bearing production to:
- Design and test new ideas quickly
- Create custom or rare parts
- Make lightweight or complex shapes
The key uses of 3D printing in bearing production involves:
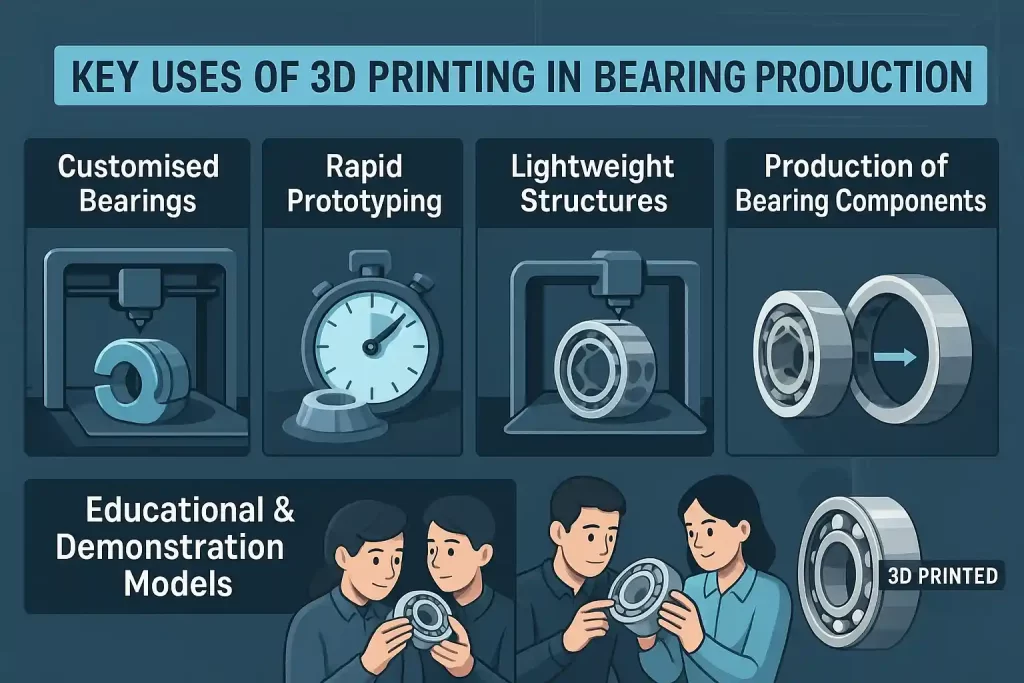
- Customised Bearings: 3D printing is widely useful for designing bearings and their components for machines and tools with unique designs and shapes. 3D printing allows for designing one of a kind bearing design that fits the custom space.
- Rapid Prototyping: Another reason behind the wide acceptance of 3D printing for bearing production is due to its ability to quickly create sample bearings to test new designs and sizes. It helps with designing a prototype bearing to be used and test fit before mass production.
- Lightweight Structures: 3D printing models allow for the creation of hollow or lattice designs that reduce weight without losing strength. These bearings are widely used in racing applications, drones, aerospace, and more.
- Educational & Demonstration Models: 3D printing is also used in the production of non-functional bearings meant for training, teaching, and exhibitions.
- Production of Bearing Components: 3D printing or additive manufacturing is also preferred to manufacture specific bearing parts like retainers, cages, housing, and more.
Low Volume Production: 3D printing of bearings is a cost-effective option for producing a small number of bearings without the need for expensive moulds or tools.
Materials Used for 3D Printed Bearings
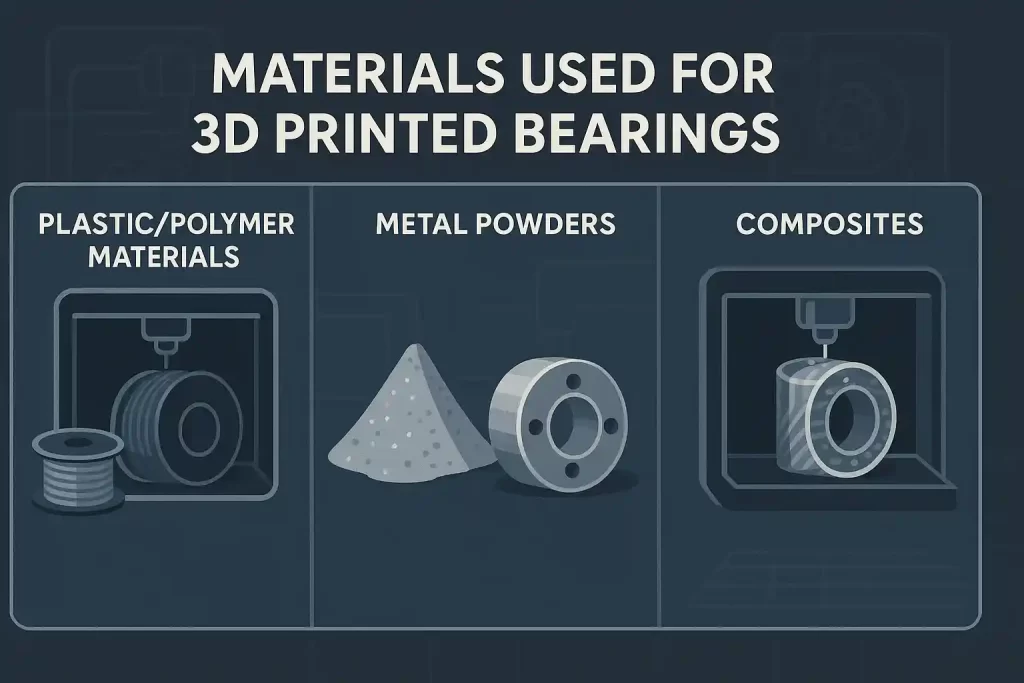
The choice of 3D printing materials depends on the type of bearing being produced and its usage – whether it is being used for prototyping, lightweight design, or actual performance testing. A 3D printing machine builds the bearing or its parts layer by layer using suitable materials. Some of the common materials used for 3D-printed bearings include:
- Plastic/Polymer Materials: Plastic or polymers are commonly used materials in 3D-printed bearings. Bearings made from plastic or polymer are lightweight, corrosion-resistant, and perfect for limited-load applications.
- Metal Powders: Metal powders including stainless steel, titanium, tool steel, aluminium, and more are used in manufacturing 3D printed bearings that are strong and durable, ideal for high-load applications.
- Resins: Resins as materials are used in high-detail 3D printing technology. Bearings designed using resins are materials that are precisely engineered, are very high on details, and have smooth surfaces. 3D printing machines like SLA, DLP, and LCD often use this material.
- Composites: Several materials are combined like materials reinforced with carbon fibre or glass fibre offering a high strength-to-weight ratio and improved wear resistance. These materials are preferred for lightweight structural parts in aerospace or robotic bearings.
Advantages of 3D Printing in Bearing Manufacturing
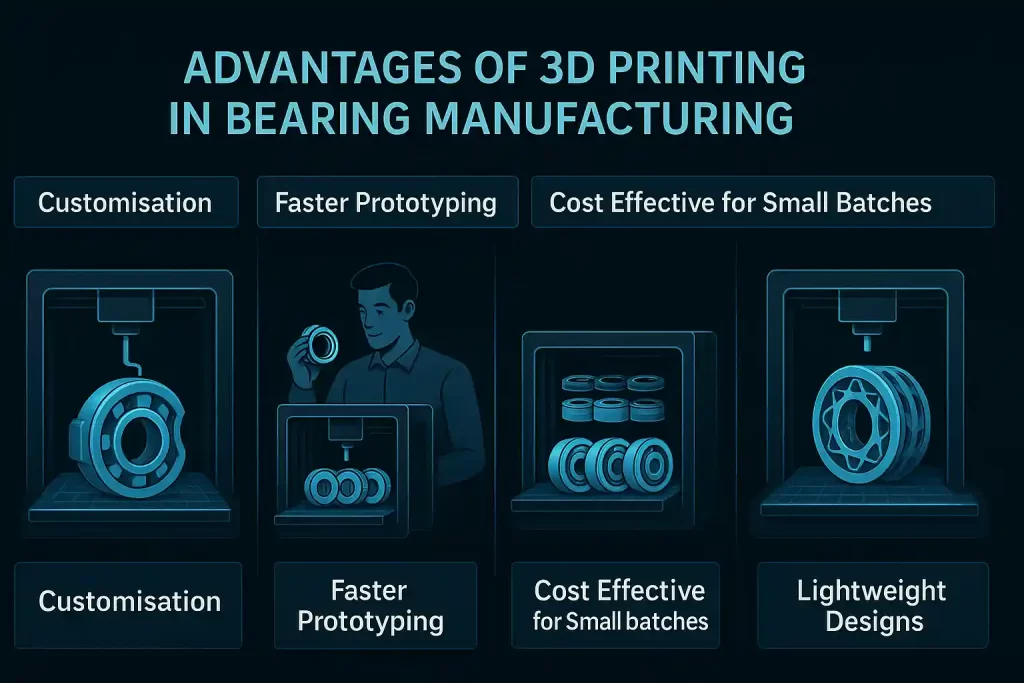
3D printing is bringing innovation and speed to how different types of bearings, like ball bearings and roller bearings, are developed and tested. While it’s not yet used for mass production, it offers several key advantages in the manufacturing process:
- Customisation: 3D printing makes it easy to design bearings in non-standard shapes or sizes for specific machines or tools. Eg: 3D printed bearings are ideal for custom applications in robotics, aerospace, medical devices, and more.
- Faster Prototyping: 3D printing allows the engineers to quickly create and test new designs for various types of bearings including ball bearings or roller bearings without waiting weeks for machining or moulding.
- Cost Effective for Small Batches: 3D printing of bearings is more cost-effective for limited production when compared to traditional methods of production. There is no need for tooling or moulds.
- Lightweight Designs: 3D printing allows hollow or lattice structures inside bearings — useful for creating lightweight ball bearings in drones or satellites.
Challenges and Limitations
While 3D printing offers many benefits in the design and development of bearings, there are some practical limitations that prevent it from fully replacing traditional manufacturing. Some of them are listed below:
Limitation |
Description |
Material Limitation |
Not all bearing materials are 3D printable, thus bearings lack load carrying capacity and durability. |
Slow for Mass Production |
3D printing can be too slow and expensive for producing large quantities, but traditional manufacturing is still effective for large-scale manufacturing. |
Post-Processing Requirements |
Printed parts often require additional steps like heat treatment, surface finishing, or assembly. |
With advances in metal 3D printing, hybrid manufacturing, and material science, the future holds promise for stronger, high-precision printed bearings. As technology evolves, 3D printing could become a key player in producing functional bearings for specialised industries like aerospace, robotics, and medical devices. 3D printing is a powerful tool for innovation in bearing manufacturing, especially for design flexibility, rapid testing, and small-scale production – with exciting potential still ahead.