Unearthing precious metals calls for some heavy duty work that needs a highly reliable set of equipment. From crushers and conveyors to drilling rigs, every bit of mining equipment requires reliable bearings that are essential for maintaining efficiency and uninterrupted functioning of mining operations.
Types of Bearings Used in the Mining Industry
- Ball Bearings: Ideal for handling lighter loads with high-speed applications, the ball bearings are often considered the backbone of the manufacturing industry and with ample reasons.
- Roller Bearings: The rollers help even distribution of heavy earth moving equipment and cranes. This is why roller bearings are suitable for heavier loads to ensure durability in tough conditions.
- Spherical Roller Bearings: Equipped with the power to handle both radial and axial loads, spherical roller bearings are perfect for correcting misalignment, especially in vibrating equipment such as drills or deep borewells.
- Tapered Roller Bearings: This has further enhanced usage especially for all sorts of heavy-duty applications, providing excellent load-carrying capacity.
- Cylindrical Roller Bearings: Known for their high radial load capacity, they are often used in conveyors and large gearboxes.
This quick guide provides an overview of bearing types, helping in selecting the right one based on load, speed, and operational conditions.
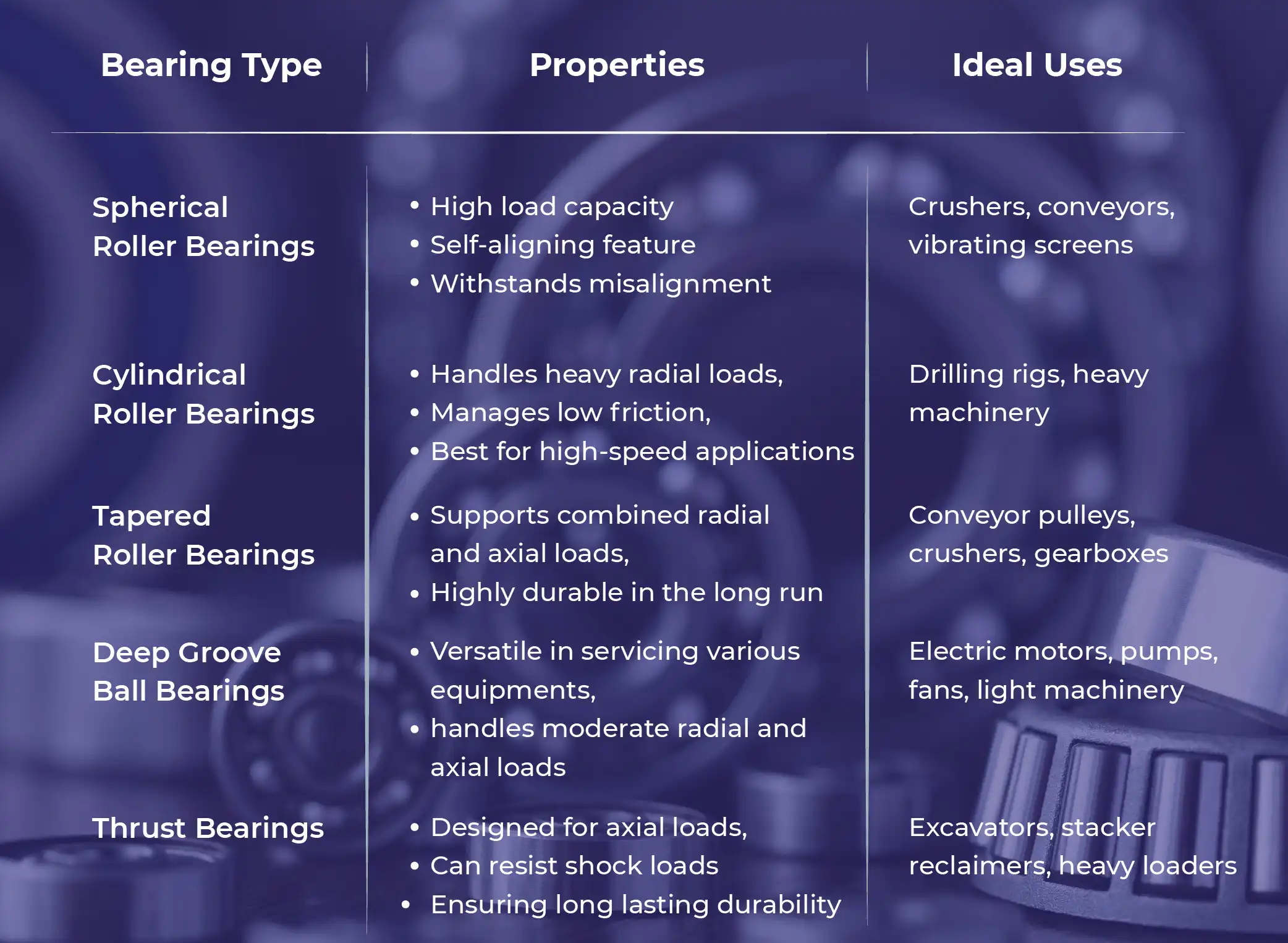
Applications of Bearings in Mining Equipment
Bearings are integral to the operation of various mining equipment, including:
- Crushers: Mining industry depends a lot on crushers. Reliable bearings installed in crushers can end up supporting massive shafts and rotating elements, which ensure consistent crushing action on site at the quarries.
- Conveyors: Conveyors move with precision in order to set up a well functioning assembly line for production. Therefore bearings in conveyor systems help facilitate smooth transport of materials, across long distances.
- Vibrating Screens: In mining a vibrating screen has special importance. Spherical roller bearings handle the intense vibrations and loads of the mining PPE to maintain consistent efficiency.
- Drilling Rigs: Mining involves excavating to a great extent and so it is not surprising that drilling rigs prefer high-performance bearings to ensure the stability and precision of drilling operations.
- Heavy Machinery: Above all else it is the heavy mining PPE which contributes the most vital aspect, its structural integrity. Bearings help shoulder the balance of heavy duty equipment such as bulldozers, loaders, and other heavy machinery.
Each application demands specific bearing characteristics, tailored to the equipment’s operational needs.
Challenges Faced by Bearings in the Mining Industry
Mining operations present unique challenges that bearings must overcome:
- Harsh Operating Conditions: Dust, dirt, moisture, and extreme temperatures are common in mining environments. This is why mining industry bearings need to be resistant to contamination and corrosion.
- Heavy Loads and High Impact: Bearings must withstand significant radial and axial loads, as well as the impact of heavy volumes from constant use. This is non negotiable and decides the longevity of the PPE.
- Continuous Operation: Mining equipment often operates non-stop, making durability and reliability crucial.
- Corrosion and Contamination: Bearings in mining environments are prone to corrosion and contamination, necessitating robust seals and protective features.
Addressing these challenges requires selecting bearings designed for durability and resilience in harsh conditions.
Selecting the Right Bearings for Mining Applications
Choosing the correct bearings is critical to ensuring optimal performance and longevity in mining operations:
- Load Capacity: Bearings must match the load requirements of the equipment, whether handling radial, axial, or combined loads.
- Speed: Bearings must maintain performance at the required operational speed without overheating or excessive friction.
- Temperature: Bearings should be capable of functioning efficiently in extreme temperatures, both high and low.
- Environmental Conditions: Bearings should be resistant to dust, dirt, moisture, and corrosive elements common in mining settings.
- Equipment Type: The specific machinery—whether crushers, conveyors, or drilling rigs—dictates the bearing type and specifications.
Considering these factors helps in selecting bearings that will perform reliably under demanding conditions.
Maintenance and Care of Bearings
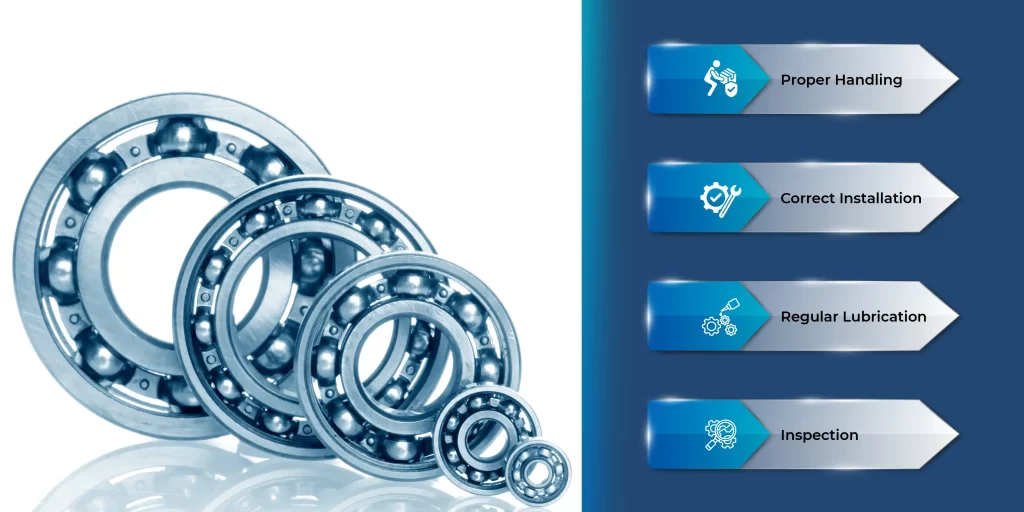
Proper maintenance is essential to extend bearing life and prevent unexpected failures:
- Routine Maintenance: Regular inspections for wear, misalignment, and lubrication levels are vital. Establishing a maintenance schedule helps in detecting issues before they lead to equipment downtime.
- Re-Greasing and Lubrication: Regular re-greasing is necessary to reduce friction and wear. Automatic lubrication systems can ensure consistent application, minimising human error.
- Cleaning and Replacing Bearings: Contaminated or damaged bearings must be cleaned or replaced promptly to prevent further equipment damage.
Maintaining a proactive approach to bearing care minimises the risk of costly downtime and repairs.
Lubrication Solutions for Mining Bearings
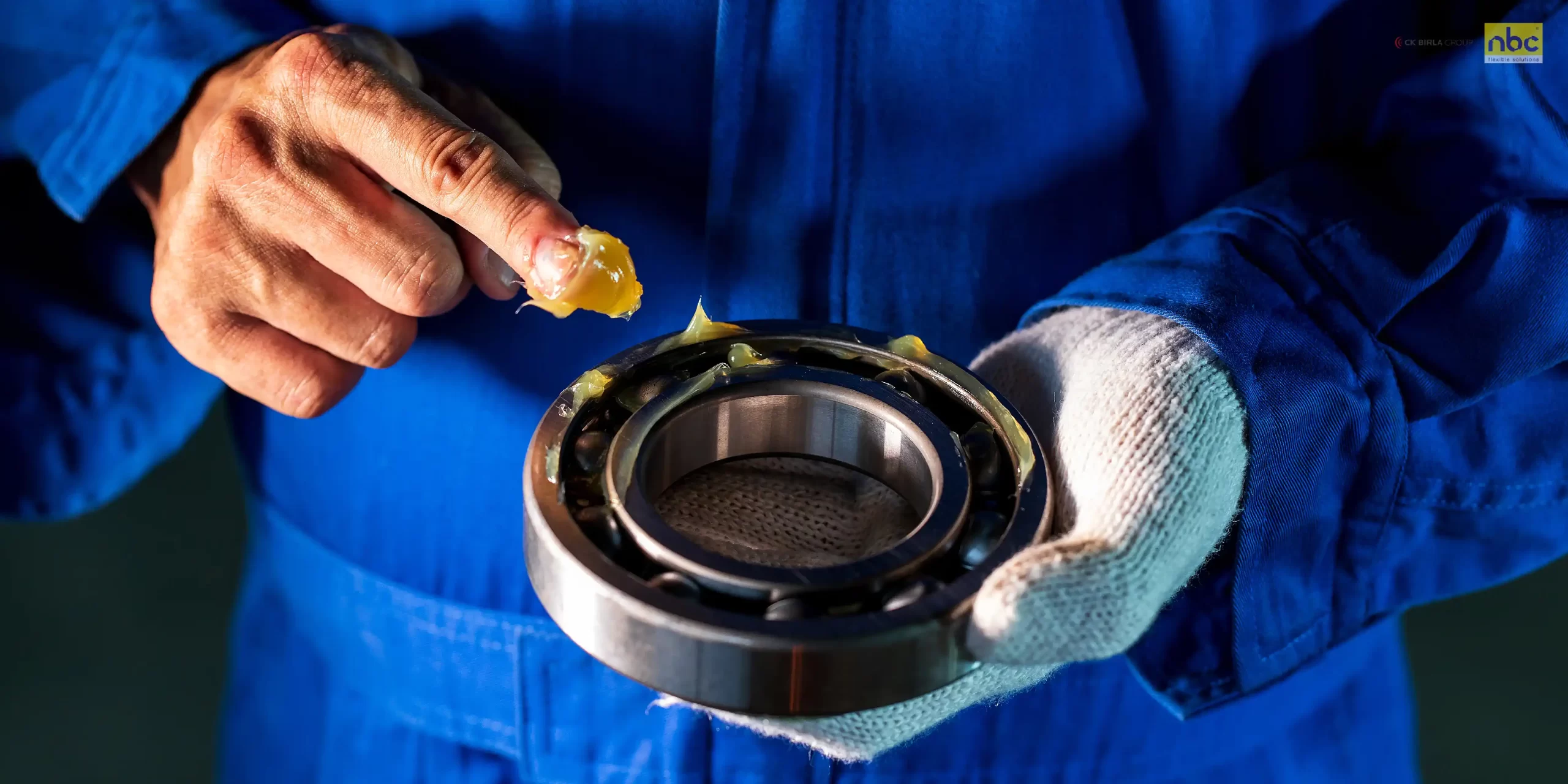
Effective lubrication is key to maximising bearing performance in mining applications:
- Types of Lubricants:
- Greases: Ideal for bearings that require long-lasting lubrication in contaminated environments.
- Oils: Suitable for high-speed or high-temperature applications, though requiring more frequent maintenance.
- Lubrication Methods:
- Manual Lubrication: Allows for precise control but can be labour-intensive.
- Automatic Lubrication Systems: Provide consistent lubrication, reducing the risk of under- or over-lubrication.
- Centralised Lubrication Systems: Efficiently lubricate multiple bearings from a single point, ideal for large-scale operations.
Selecting the appropriate lubrication method and type ensures the longevity and efficiency of bearings in mining equipment
Conclusion
Bearings are fundamental to the mining industry, supporting the operation of critical machinery in challenging environments. By selecting the right bearings, maintaining them properly, and using effective lubrication solutions, mining operations can achieve greater efficiency, reduce downtime, and extend the lifespan of their equipment. As the industry evolves, advancements in bearing technology will continue to enhance the productivity and sustainability of mining operations.
FAQ's
What types of bearings are used in mining?
Mining applications mainly use bearings which are helpful in moving heavy things. The four most sought after bearings in the mining industry are:
- spherical roller bearings,
- tapered roller bearings,
- cylindrical roller bearings, and
- ball bearings.
How are bearings utilized in various industries?
Bearings are crucial in many industries. The main utility of reliable bearings include
- supporting the rotational or linear movement of machine components
- reducing friction between moving parts, for smooth & efficient operations.
What is the primary function of bearings?
Bearings are designed to optimise the use of heavy duty mining PPE.
- minimise friction between moving parts
- allow smooth and efficient movement
- support loads (radial, axial, or both) and
- guide the motion within machines to improve efficiency, and
- reduce overall energy usage.
Which bearing type is most commonly used?
- Ball bearings are among the most widely used bearing types due to their versatility, moderate load capacity, and suitability for high-speed applications. They are prevalent in numerous industries, including mining PPE.
- Spherical roller bearings are also commonly used in heavy-duty mining applications.