Lubrication is the lifeblood of machinery, especially when it comes to bearings. Proper lubrication plays a critical role in reducing friction, dissipating heat, and preventing wear and tear, ultimately prolonging the lifespan of bearings and ensuring optimal performance.
What is the importance of Lubrication for Machines?
Lubrication is essential for maintaining the health and efficiency of machinery, particularly bearings, which are subjected to high levels of friction and stress during operation. Without proper lubrication, bearings can experience
- Excessive wear,
- Overheating,
- Premature failure,
- Costly downtime and repairs.
Effective lubrication forms a protective barrier between moving parts, reducing friction and minimizing the risk of metal-to-metal contact, corrosion, and damage.
What are the Types of Available Lubricants for Bearings?
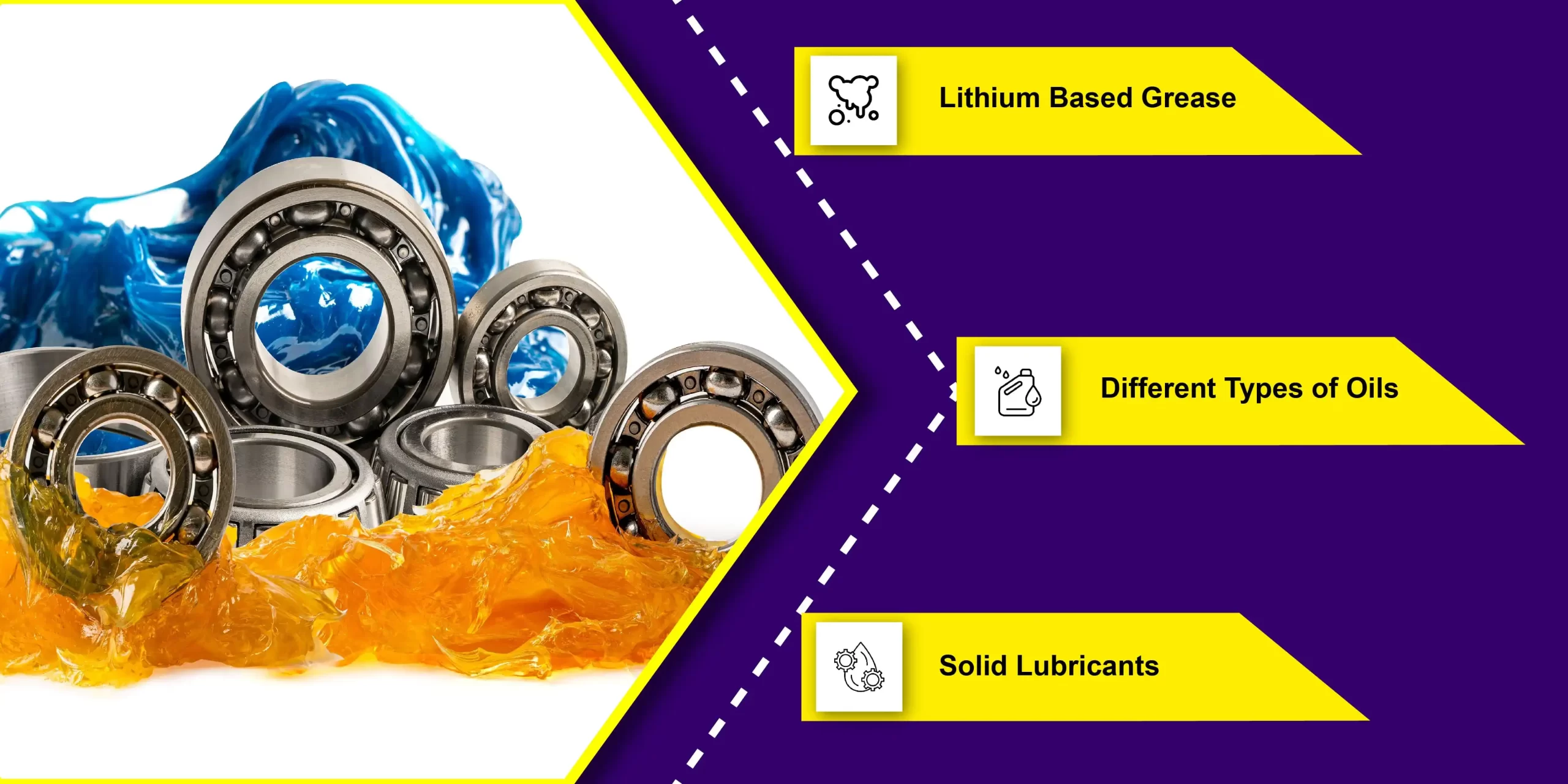
Various types of lubricants are available for bearings, each offering specific properties and benefits suited to different applications and operating conditions. Common lubricants include:
- Lithium based grease: These are a popular choice for their viscosity and adherence to bearing surfaces,
- Different types of oils: These provide excellent lubrication in high speed and high temperature environments, and
- Solid lubricants: For example graphite and molybdenum disulfide (MoS2) lubricants offer long-lasting lubrication and are ideal for applications where traditional lubricants may not be suitable.
What are the Factors for Selecting the Right Lubrication?
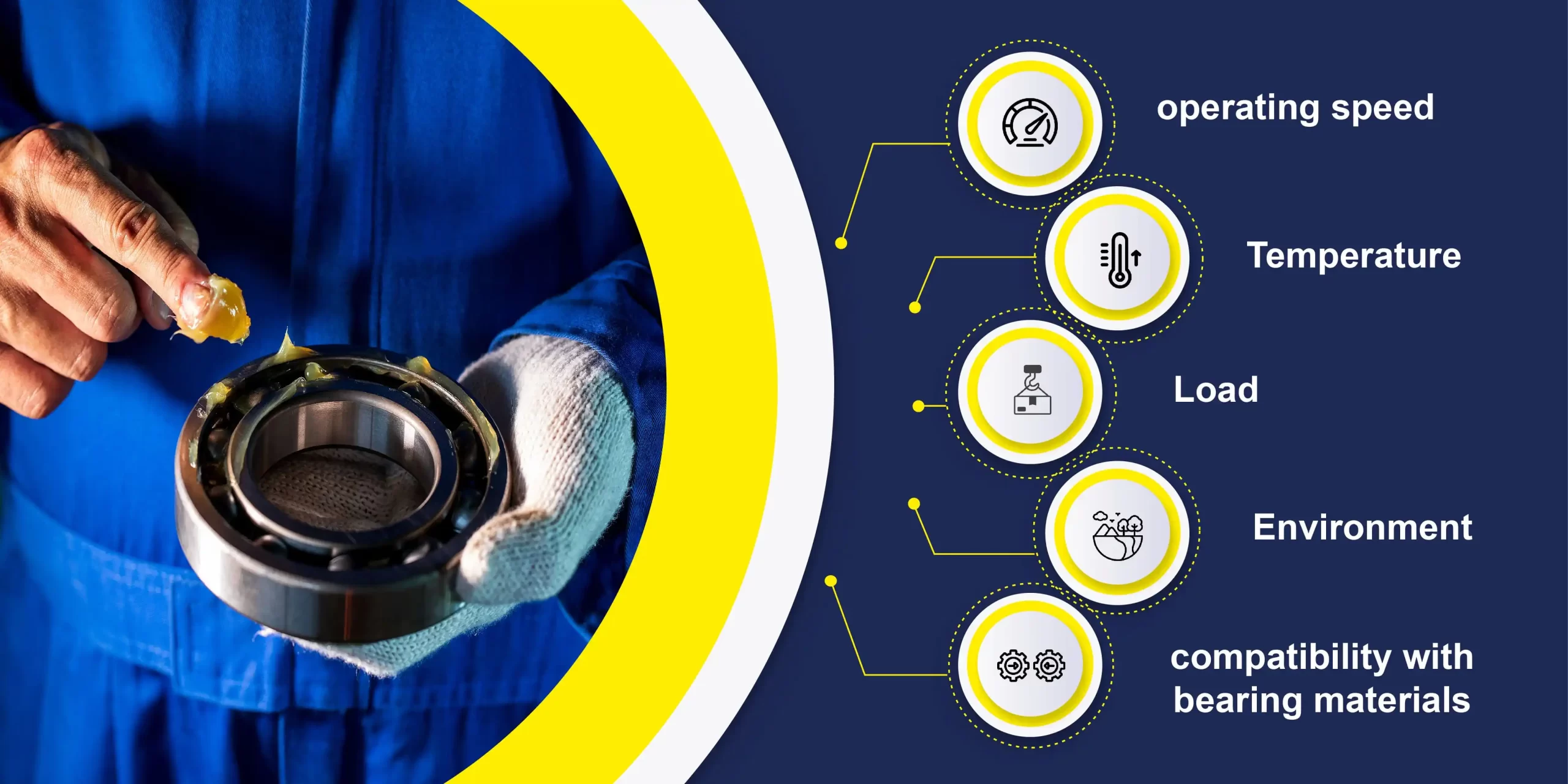
When selecting the right lubrication for bearings, several factors must be considered to ensure optimal performance and longevity. These factors include
- Operating speed,
- Temperature,
- Load,
- Environment, and
- Compatibility with Bearing materials.
For example, Fluorosilicone oil, when thickened with a fluorinated polymer, is ideal lubrication for ball bearings that operate in high load, high speed and high temperature.
What are the Best Practices for Lubricating Bearings?
To maximize bearing longevity and performance, it’s crucial to adhere to best practices for lubricating bearings. This includes establishing a regular maintenance schedule to monitor lubricant levels, cleanliness, and condition.
Bearings should be properly cleaned and inspected before relubrication to remove contaminants and ensure optimal lubricant distribution.
Additionally, using the correct amount of lubricant and applying it evenly across bearing surfaces is essential for effective lubrication and preventing over-lubrication or under-lubrication issues.
FAQ's
What is the best lubricant for bearings?
The best lubricant for bearings depends on various factors such as operating conditions, load, speed, and environment. Grease and oil are commonly used lubricants for bearings, with each offering specific advantages. Grease is preferred for its ability to stay in place and provide long-lasting lubrication, while oil offers excellent heat dissipation and lubrication in high-speed applications.
What lubricates bearings?
Bearings are lubricated using various types of lubricants, including grease and oil. These lubricants form a thin film between bearing surfaces, reducing friction and wear, dissipating heat, and preventing corrosion. Proper lubrication ensures smooth operation, extends bearing life, and minimizes the risk of premature failure.
How are main bearings lubricated?
Main bearings are lubricated using either grease or oil, depending on the application and operating conditions. Grease is commonly used for its convenience and ability to stay in place, while oil is preferred for applications requiring high-speed or high-temperature operation. Lubrication is typically applied through centralized lubrication systems or manual greasing/oiling procedures.
Are all bearings lubricated?
Yes, all bearings require lubrication to operate effectively and maintain optimal performance and longevity. Lubrication reduces friction between bearing surfaces, prevents wear and corrosion, and dissipates heat generated during operation. Proper lubrication is essential for ensuring smooth operation, minimizing maintenance requirements, and extending bearing life.
What is the viscosity of oil for bearings?
The viscosity of oil for bearings varies depending on factors such as operating speed, temperature, load, and bearing type. Oil viscosity is typically measured in centistokes (cSt) or Saybolt Universal Seconds (SUS) at a specific temperature. The appropriate oil viscosity for bearings is determined based on manufacturer recommendations, bearing size, and operating conditions to ensure adequate lubrication and protection against wear and friction.