With Finite Element Analysis, materials and products can be predicted to respond to forces in the real world as well as other physical factors such as vibrations, heat, and fluid flow using statics. The FEA process helps to demonstrate whether the product will work or not. A product needs to be examined if it does not sustain the conditions under which it must function. Therefore, the advantage of FEA is that the company doesn’t have to manufacture the product at this stage.
How do FEA Elements Work?
For finite element analysis to function, an object must be divided into numerous smaller constituent parts, often known as “finite elements”. In other words, the more elements, the finer the mesh, which results in an accurate model. It is possible to exactly predict how the product will respond to various simultaneous inputs by using complicated mathematical equations. Thanks to modern software, and automated processes, with FE this mathematical calculation can be carried out easily and quickly.
How does FEA Play a Significant Role in Optimizing the Design of Wheel Bearings?
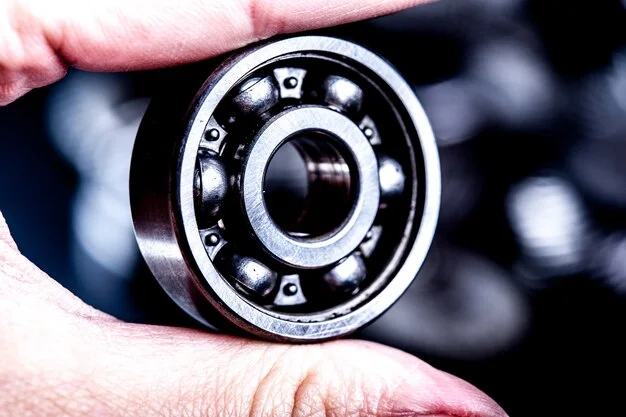
Automobile wheels are critical parts, and their strength is essential for safety. The car’s wheels move in a circular motion as it travels; thus they bear both the vehicle’s radial load and its bending load. The standard design approach involves using FEM to analyze wheel forces. After creating the model and determining the load, the force division situation and dynamic response may be obtained, allowing the calculation of extreme failure position and dangerous point. During driving, the wheels must be strong enough to run on rough roads. At the same time, it is important to meet the profit by minimizing the costs. Rotating wheels get two different impacts from radical and bending 0.
What is the Stiffness of the Wheel Bearing?
The relation between an element’s deformation and the application of external loads to the component is what gives the stiffness concept its name: F = k? Where F is, being force applied, k stiffness of the component, and ? the deformation. This link between force and deformation is normally created in the matrix form by: {F1} = [k -k] {F2} = [-k k] With F1 and F2, being the applied forces, 1, and 2 resulting in deformation in nodes 1 and 2.
Although the stiffness matrix of a double-row angular contact ball bearing is seemingly more difficult. There are numerous publications with various mathematical models and examined bearing design geometry. The nonlinear contact characteristics inside the roller bearing are the cause of major complexity, which makes the bearing stiffness nonlinear, and load-dependent.
In the most recent publication, a 5*5 stiffness matrix is used to define bearing stiffness for a defined loading condition. For double-row bearings, the stiffness may either be identified by two matrices, or by one stiffness matrix for double-row units. Under dynamic operating conditions, the bearing must maintain a camber angle within relevant limits. Depending on the bearing rigidity or stiffness specified by the customer, under a specified bending moment. Bearing mounting flange, internal construction, etc., are designed. Following the evaluation of the bearing stiffness by FEA technology, the design is further improved. FEA Technology satisfies the stiffness requirements of the customer as well as the bearing weight, life, packing, etc. The bearing stiffness is tested using the Test Setup. Verified concerning the FEA calculation once the prototype is complete.
Why is Bearing Stiffness Critical to Vehicle Dynamics?
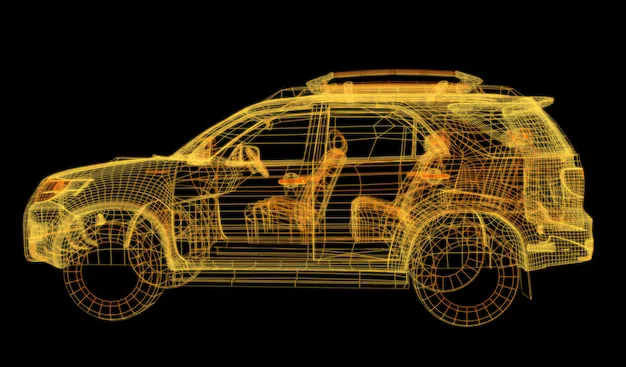
An angle made by the vertical axis of the wheel and the vertical axis of the vehicle is called a cambre angle. It is visible from the rearview mirror; it is an angle made by the vertical axis of the wheel and the vertical axis of the vehicle. Specifically designed for the steering and suspension. Cambre angle directly affects tyre wear. Since improper camber angle adjustment could result in excessive inner or outer tread wear.
Vehicle dynamics qualities can be further broken down into handling, steering, and ride comfort, which are important for the customer’s driving experience. It is important to understand stiffness in vehicle dynamics as this correlates with vehicle performance. The tests satisfactorily showed that the bearing could withstand the load and avoid making contact with the air gap, which was the primary goal. Furthermore, bearing deflection tests were conducted before and after fatigue tests.
In the tests, no hub bearing damage was observed, which is essential for determining product longevity and maintenance intervals.
Understanding Finite Element Analysis:
It is a technique for forecasting how a material or object will respond to forces, heat, vibrations, and other physical effects. By dissecting intricate shapes into simpler components called elements the method facilitates the analysis of the structure’s behavior. The concept of FEA focuses on breaking down complex problems into smaller, simpler parts to make calculations easier.
The Mathematics Behind FEA:
- Nodes: Nodes are sometimes referred to as the backbone of FEA, without them the analysis won’t work. They are the points in the structure where the calculations are performed.
- Elements: Elements are the puzzle pieces, they are the building blocks that make up a complex shape.
- Meshing: The process of breaking down a complex shape into smaller simpler pieces (elements) to facilitate calculations is called meshing and it’s similar to turning a large puzzle into tiny pieces.
Steps Involved in Finite Element Analysis:
1. Pre-Processing: Preprocessing is the first step involving creating or importing a CAD (computer-aided design) model of the part or structure.
2. Meshing: This is the second step involving dividing the model into smaller elements.
3. Solving: In this step, the computer calculates how the structure behaves under the applied loads. Solving follows a principle:
[K]{U}={F}
K = Stiffness matrix (material & shape properties)
U = Unknown displacement
F = Applied force
4. Post Processing: This is the final step and involves stress & strain calculation of each element and interpreting the results.
Applications of Finite Element Analysis:
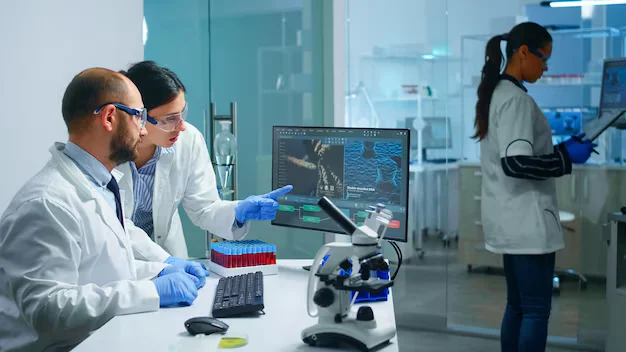
- Aerospace: Finite element analysis plays a critical role in the aerospace industry in ensuring wing strength, analysing airflow around the wings, and to also analyse if the aircraft can take on extreme temperatures. Boeing, an aircraft manufacturer tests its aircraft components using FEA prior to launch.
- Automotive: In the automotive sector finite element analysis is frequently used to simulate car crashes in order to improve safety, analyse aerodynamics, and ensure engine longevity under forces and vibration.
- Civil Engineering: In the field of civil engineering and construction FEA is crucial for guaranteeing that structures such as bridges, buildings, etc are strong enough to withstand loads, wind, earthquakes, etc.
- Biomedical Engineering: FEA is used in the biomedical engineering industry to help design long-lasting and lightweight implants and medical equipment. For example, to make sure a hip implant won’t break it can be tested using FEA to simulate walking, running, sitting, and jumping.
FEA Software and Tools:
- ANSYS: It is the most widely used software tool for finite element analysis. ANSYS is known for its versatility across different analysis types like structural, thermal, fluid dynamics, and electromagnetic.
- Abaqus: Abaqus is widely used in automobiles, aerospace, energy, and biomedical engineering industries. Abaqus is known for advanced tools for simulation, analysis, and optimization.
- COMSOL Multiphysics: It is a popular and incredibly flexible simulation program made for multiphysics simulations.
FAQ's
What is the purpose of FEA?
FEA is a technique for checking how a material or object will respond to forces, heat, vibrations, and other physical effects.
What is the difference between FEA and FEM?
FEM (finite element method) is a mathematical technique, while FEA is the process of using FEM to simulate a behaviour.
What is meant by finite element analysis?
The finite element analysis process helps to demonstrate whether the product will work or not.
What type of analysis is FEA?
FEA is a type of numerical analysis.
What are FEA tools?
There are various types of FEA tools. ANSYS, Abaqus, and COMSOL Multiphysics are some of the commonly used ones.
What is the purpose of FEA?
FEA is a technique for checking how a material or object will respond to forces, heat, vibrations, and other physical effects.