The elementary significance of bearings in the industrial landscape cannot be overstated. Machineries across industries depend upon their optimal functioning for the overall consistency in performance of various mechanical systems. But like all other components, bearings are also susceptible to wear and tear, and the consequences of undetected faults in this case can be substantial, ranging from unplanned downtime to increased maintenance costs and, in severe cases, damage to other critical components.
What is the Significance of Bearing Fault Detection?
Healthy and functional bearings are at the core of operational efficiency across the industrial landscape. The health of bearings are subject to various stresses, including loads, speeds, and environmental conditions. While bearings are designed to withstand these challenges, factors such as wear, misalignment, imbalance, and lubrication issues can lead to faults. Recognizing the significance of bearing fault detection becomes imperative as it forms the frontline defense against operational disruptions. By recognising the faults will there be appropriate controls and safety measures in place to keep the downtime to the minimum.
What are some common Bearing Faults and how to identify them?
To effectively implement fault detection techniques, a comprehensive understanding of common bearing faults and their indicators is essential. Bearing faults can manifest in various forms. Here is a snapshot of the various possible faults and their indicators:
Types of bearing faults | Indicators or signs of fault in bearings |
Bearing Wear | Gradual increase in temperature and vibration levels. |
Bearing Misalignment | Unusual noise during operation and irregular wear patterns. |
Bearing Imbalance | Vibration, especially during high-speed rotations. |
Lubrication Problems | Increased operating temperature and changes in friction characteristics. |
Traditional Methods vs. Advanced Techniques of bearing fault management
Historically, bearing health was monitored through periodic inspections and manual monitoring. This meant running physical inspections which were not only tedious but also time and cost consuming. They also lacked the real-time capabilities needed for proactive intervention. With the need for quick turnaround advanced techniques came into being, which leverage cutting-edge technologies to enable continuous, real-time assessment of bearing health.
Among current techniques, vibration analysis stands out as a powerful tool for bearing fault detection. The principle behind vibration analysis is identification of irregularities in bearing operations that produce distinct vibrational patterns. There are mainly two approaches to vibration analysis:
- Using advanced vibration sensors, i.e., high-tech sensors capable of detecting subtle vibrations, even in the early stages of fault development.
- Identifying specific frequencies associated with different types of bearing faults, allowing for precise and timely diagnosis, supported by adequate preparedness. .
The transition from traditional methods to advanced techniques represents a paradigm shift in the approach to maintenance and reliability.
Benefits of Early Fault Detection:
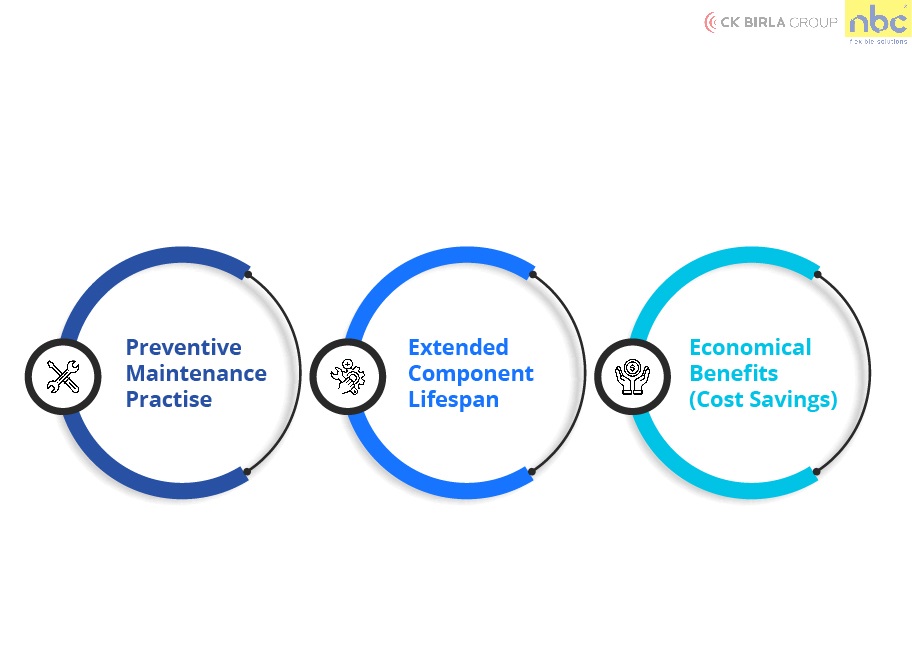
With the implementation of robust fault detection techniques, particularly through vibration analysis as discussed above, there have been some notable benefits for industrial operations:
- Preventive Maintenance Practise: Early fault detection ensures proactive measures, preventing unexpected breakdowns and minimizing downtime.
- Extended Component Lifespan: Timely identification and intervention in bearing faults contribute to a prolonged lifespan of the components.
- Economical Benefits (Cost Savings): By avoiding costly breakdowns and reducing overall maintenance expenses, early fault detection translates into significant cost savings across the industrial landscape.
Implementing Fault Detection Techniques:
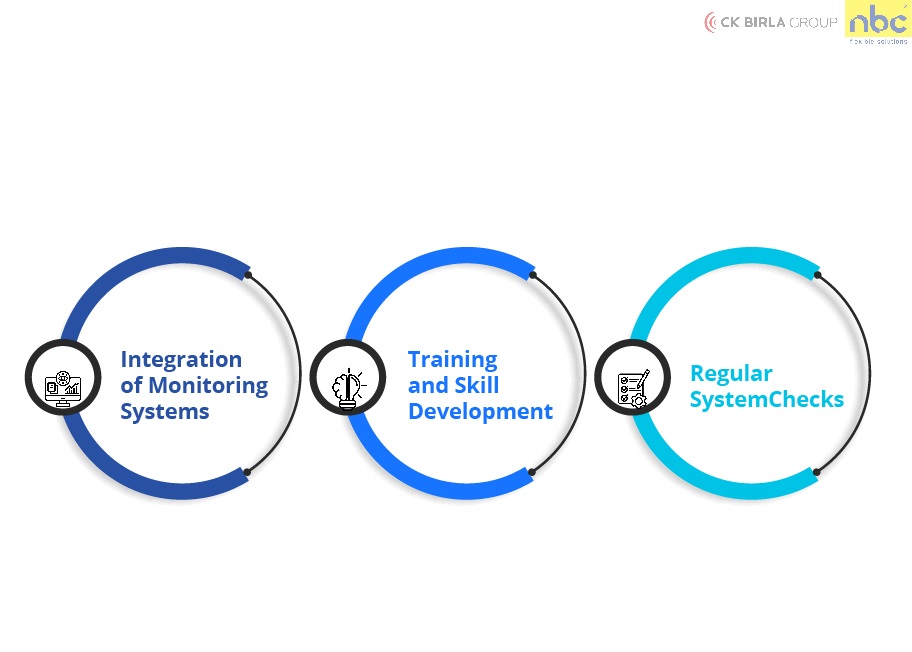
While the benefits of early fault detection are evident, their success depends on the effective implementation of these techniques in a strategic way. The following approaches have proved to be effective:
- Integration of Monitoring Systems: Installation of advanced condition monitoring systems provide continuous, real-time assessments of bearing health.
- Training and Skill Development: A big part of implementation depends on the personnel in charge of interpreting monitoring system outputs and making informed actions. Their skillset is of prime importance for sustained efficiency.
- Regular System Checks: Establishing routine system checks and calibration of monitoring equipment on a timely basis, is a best practice that will definitely ensure accuracy in the long run.
FAQ's
What benefits can businesses expect from early detection of bearing faults?
Early detection allows businesses to
- address issues proactively,
- reducing downtime,
- minimising repair costs, and
- extending the overall lifespan of machinery.
What role does oil analysis play in ensuring the health of bearings?
Oil analysis helps identify contaminants, wear particles, and lubricant condition, providing insights into the health of bearings and enabling timely maintenance.
Are there any industry-specific considerations for implementing these fault detection techniques?
Yes, industries may have unique operational conditions. Tailoring fault detection techniques to specific industry needs ensures accurate and effective monitoring.
How does infrared thermography help in assessing the health of bearings?
Infrared thermography detects temperature variations, revealing potential issues like overheating in bearings, allowing for preventive measures before serious faults occur.
What traditional methods are used for bearing inspection and monitoring?
Traditional methods include visual inspection, vibration analysis, and acoustic monitoring. These methods, combined with modern techniques, provide a comprehensive approach to bearing health assessment.