Industries work on the efficiency of machineries that perform a large chunk of the work in the factories. Responsible for facilitating smooth movement and reducing friction between moving parts, bearings across industries like construction, mining, and manufacturing, the reliability of bearings directly impacts performance, safety, and the service life of the machinery.
These machines operate mostly under high stress and demanding conditions. Good quality bearings ensure durability to handle heavy loads, reduce friction, and maintain smooth movement.
In environments such as mining or construction, where equipment operates for long hours under extreme conditions, bearings not only impact machine performance but also costs of maintenance.
Which is why having reliable bearings are vital to counter equipment breakdowns, production downtime, safety hazards and eliminate a majority of possible hurdles to productivity.
Types of Bearings Used in Heavy Machinery
Heavy machinery relies on various types of bearings, each of which is customised to deal with some specific operational conditions.
Type of Bearing |
Features |
Application |
Ball Bearings |
Sustains high speed with low friction |
Commonly used in smaller machinery components. |
Tapered Roller Bearings |
Designed for radial and axial loads |
Ideal for heavy machinery like cranes and excavators |
Spherical Roller Bearings |
Handle heavy loads which have a potentially high risk of misalignment |
Used in mining and construction equipment. |
Cylindrical Roller Bearings |
Also known to manage heavy radial loads using the roller mechanism |
Suitable for conveyor systems and large motors. |
Thrust Bearings |
Helps manage heavy axial loads. |
Used in hydraulic systems and heavy-duty pumps. |
Proper selection is crucial for ensuring the long-term reliability of each of these bearings in heavy machinery applications.
Key Factors Affecting Bearing Reliability
- Load and Stress: Although moist bearings are designed to handle loads, excessive loads can lead to deformation of the bearing itself.
- Lubrication: Lubrication works to minimise friction between the bearing components. Therefore, insufficient lubrication can lead to friction damage by overheating. Over-lubrication can attract contamination and other issues.
- Contamination: Contaminants such as dirt, dust, and moisture can enter the bearing, causing corrosion and abrasion. This affects the bearing surface. Sealed bearings or protective shields can help contain contamination to minimal..
- Temperature: Extreme temperatures cause thermal expansion, or lubricant thickening depending on how high or low the operating temperature is. Both these signs end up causing misalignment and damage to the bearing components.
- Installation: Improper installation is linked to misalignment, excessive force, or incorrect installation tools. Keeping a check on these will prevent deformation and premature wear.
Best Practices for Enhancing Bearing Reliability
- Proper Selection: Choosing the right bearing for the specific application is the first step in ensuring reliability.
- Correct Installation: Correct installation ensures that bearings perform as expected. It will include the following steps:
- Preparation: Cleaning the bearing and its components to prevent contamination.
-
- Alignment: Place the bearing in correct alignment with its shaft and housing components.
-
- Tools: Use hydraulic presses or bearing heaters to avoid installation damage.
-
- Tightening: Apply the correct torque when tightening bolts or fasteners to prevent misalignment.
- Effective Lubrication: Proper lubrication is essential for reducing friction and preventing wear. The right lubricant will definitely lend a long service life to the bearings.
- Regular Maintenance: Scheduled maintenance is critical to extending bearing life. Regular cleaning and re-lubrication prevents potential issues from becoming serious problems.
- Condition Monitoring: Condition monitoring tools, such as vibration analysis and temperature monitoring, can help predict bearing failures before they occur. It is a proactive tool to reduce risk of unexpected downtime.
Common Bearing Failures and Their Causes
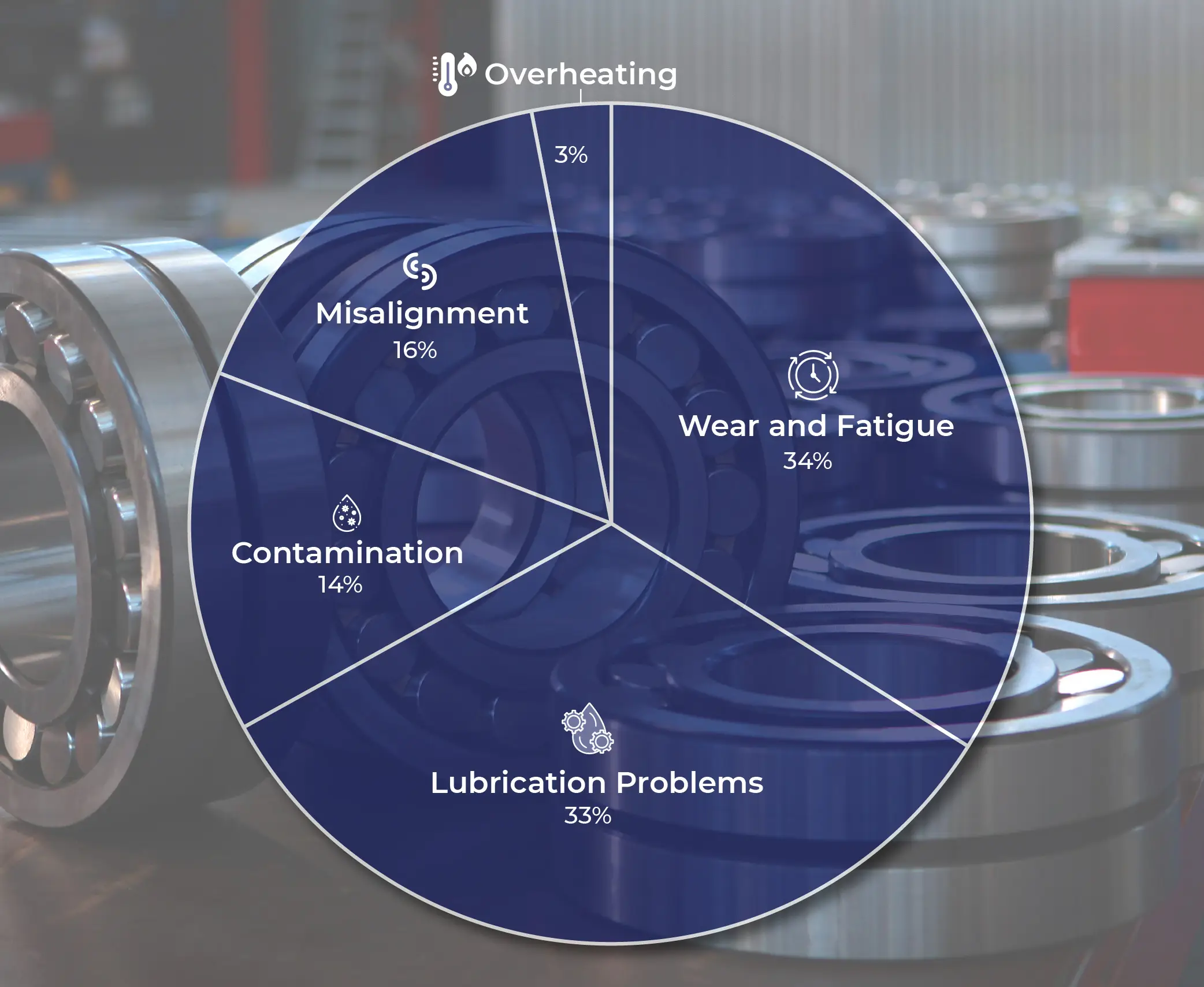
- Wear and Fatigue: 34% Bearings fail due to reaching their natural lifecycle or being subjected to high loads and stresses over time.
- Lubrication Problems: 33% bearings with improper lubrication lead to overheating and damage.
- Contamination: 14% of compromised bearings are a result of dirt, moisture, and dust, thanks to inadequate sealing.
- Misalignment: 16% Incorrect installation or operational mishandling leads to uneven load distribution and premature wear.
- Overheating: 3% of most Bearings operating in high-temperature environments expand and fail due to thermal stress.
Source: These figures reflect industry data from major reports and failure analysis guides, including those from SKF and Acorn Industrial Services.
Several industries function with heavy machinery and therefore are dependent on reliable bearing performance. These industries apply the above best practices that help them tide over the possible onslaught of bearing failure. Here are some examples:
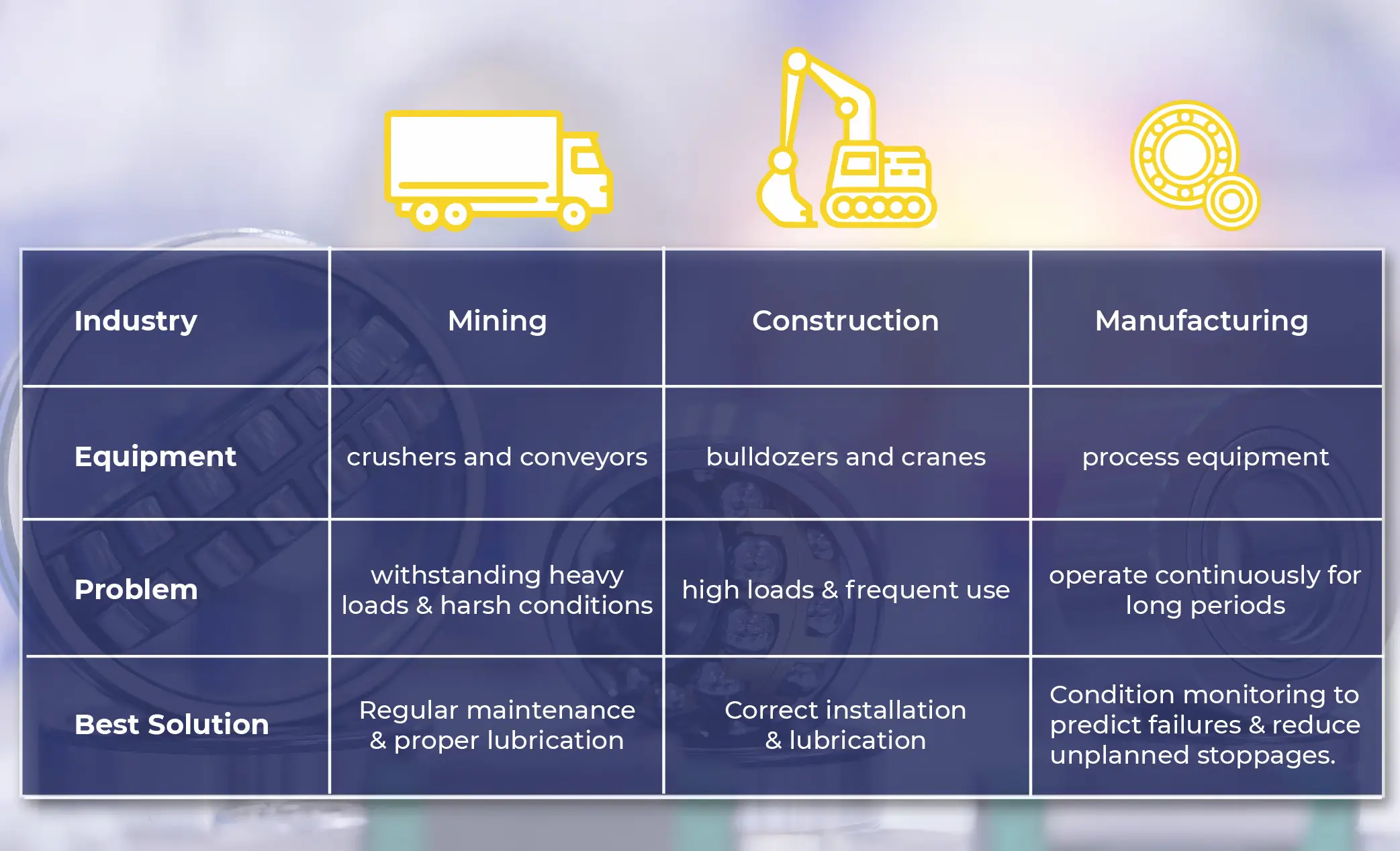
By focusing on proper selection, installation, lubrication, and maintenance, companies can ensure that their bearings remain reliable, leading to longer machinery life, fewer breakdowns, and reduced operational costs.
FAQ's
What is the rating life of bearings?
The rating life of a bearing = Total number of revolutions before under a specific load, until it shows signs of fatigue.
How to increase bearing life?
Proper lubrication, correct installation, regular maintenance, and condition monitoring can all help extend bearing life.
How to calculate bearing life?
Based on factors like load, speed, and operational conditions using industry-standard formulas such as the L10 life calculation.
What is the biggest cause of bearing failure?
Improper lubrication is the most common cause of bearing failure, leading to increased friction and wear.
What is bearing lifespan?
The lifespan of a bearing depends on its operating conditions, load, lubrication, and maintenance practices, but typically ranges from several months to several years.